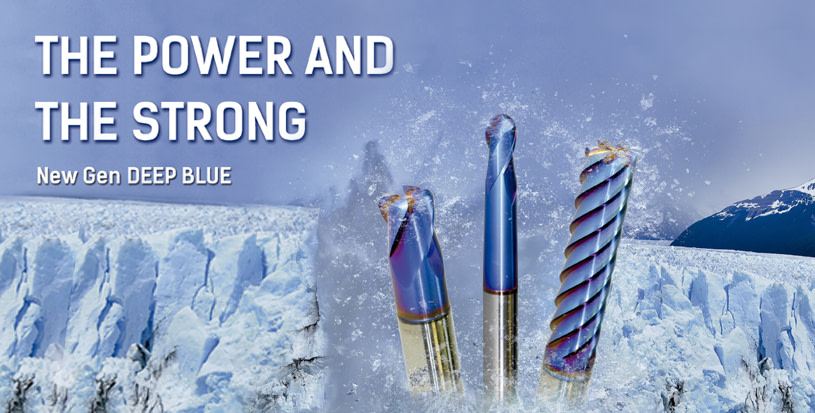
Cutting cost reduction of machining bias gears. Heli Motion 926505 and 926403
Our customer from Romania shares the success obtained in the machining process of a 50CrV4 mild steel with surface hardness from 47 to 53 HRC in a Chiron machine.
The forecast for 2020 is to produce around 1,4 million parts
A bias gear arrives as a half-finished, stamped part from, the material is spring steel 50CrV4. The gears are heat treated, resulting in a surface hardness of 47 to 53 HRC. The next process step is the machining operation. This is done on Chiron machines and consists of milling the Pitch Circle Diameter (PCD) (fig. 1 & fig. 2), the ’hook’ radius (fig. 3) and bridge cutting (fig. 4).
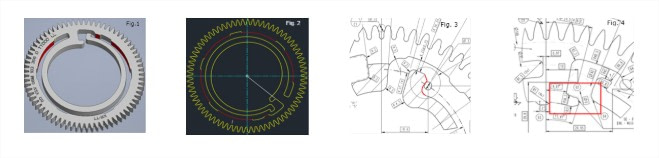
The improvement project was driven by the high cutting costs of machining center operations. They were exceeding the project goal (D4 values) with around 50%! The goal of the project was to reduce the cutting costs by 30% for all bias gear part numbers.
50% reduction in the cost of machining thanks to the new and exclusive Deep Blue PVD coating that combines carbide with a smaller micrograin subgrain and with less cobalt.
This product has a harder coating, improved dimensional tolerance, a much better tool life, hardening substrate and heat resistance substrate.
TEST & RESULTS
Depending on the bias gear’s dimension and requirements, milling cutters with different diameters are used. Initial tests were done with three tools from every diameter: end mill ∅3, ∅4, and ∅5.
Cutting conditions and parameters used for the test were the same as for the actual tool.
The main criteria to evaluate the success of the test were:
• Surface roughness
• Burr size
• Quality of the part
LIFE OF THE TOOL
The tools have been monitored after every 100 pieces. The initial tool life was set at 350 pieces and once this was reached, extra 100 cycles where added after each good measurement. The maximum tool life achieved by all test tools was around 900 pieces. Next step was to conduct a larger test using 10 end mill tools from every diameter to determine the optimal tool life in order to have a stable process and good quality.
Based on this results the production tool life for Hellion mils was set at:
• End mill ∅3 tool life = 700 pcs – actual tool life 250 pcs
• End mill ∅4 tool life = 800 pcs – actual tool life 400 pcs
• End mill ∅5 tool life = 800 pcs – actual tool life 400 pcs
Milling tool wear after completing tool life.
WHAT WERE THE OBSTACLES OR THE KEY ELEMENTS FOR THIS SUCCESS?
One of the key elements of this success is the concentricity of the tool that should not exceed 5 microns. Meeting this requirement will extend the tool life and promote excellent surface finish quality.
· Solid carbide substrate with a high hardness and good toughness.
· Coatings and cutting geometries that are matched to the material hardness.
FINAL RESULTS
The tool cost improvement is significant for all projects by changing to Helion mill tools. The yearly saving is exceeding the project target of 30%.
· The improvement will be duplicated on further 3 existing machines in VCST-BE
Access the product sheet through our ONLINE STORE... References available for inmediate delivery
Tool 926505
Tool 926403
Who can be contacted for more details? Laia Miralta l.miralta@helion-tools.com
Our customer from Romania shares the success obtained in the machining process of a 50CrV4 mild steel with surface hardness from 47 to 53 HRC in a Chiron machine.
The forecast for 2020 is to produce around 1,4 million parts
A bias gear arrives as a half-finished, stamped part from, the material is spring steel 50CrV4. The gears are heat treated, resulting in a surface hardness of 47 to 53 HRC. The next process step is the machining operation. This is done on Chiron machines and consists of milling the Pitch Circle Diameter (PCD) (fig. 1 & fig. 2), the ’hook’ radius (fig. 3) and bridge cutting (fig. 4).
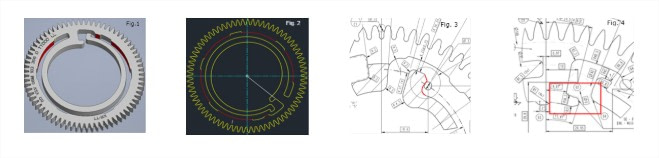
The improvement project was driven by the high cutting costs of machining center operations. They were exceeding the project goal (D4 values) with around 50%! The goal of the project was to reduce the cutting costs by 30% for all bias gear part numbers.
50% reduction in the cost of machining thanks to the new and exclusive Deep Blue PVD coating that combines carbide with a smaller micrograin subgrain and with less cobalt.
This product has a harder coating, improved dimensional tolerance, a much better tool life, hardening substrate and heat resistance substrate.
TEST & RESULTS
Depending on the bias gear’s dimension and requirements, milling cutters with different diameters are used. Initial tests were done with three tools from every diameter: end mill ∅3, ∅4, and ∅5.
Cutting conditions and parameters used for the test were the same as for the actual tool.
The main criteria to evaluate the success of the test were:
• Surface roughness
• Burr size
• Quality of the part
LIFE OF THE TOOL
The tools have been monitored after every 100 pieces. The initial tool life was set at 350 pieces and once this was reached, extra 100 cycles where added after each good measurement. The maximum tool life achieved by all test tools was around 900 pieces. Next step was to conduct a larger test using 10 end mill tools from every diameter to determine the optimal tool life in order to have a stable process and good quality.
Based on this results the production tool life for Hellion mils was set at:
• End mill ∅3 tool life = 700 pcs – actual tool life 250 pcs
• End mill ∅4 tool life = 800 pcs – actual tool life 400 pcs
• End mill ∅5 tool life = 800 pcs – actual tool life 400 pcs
Milling tool wear after completing tool life.
WHAT WERE THE OBSTACLES OR THE KEY ELEMENTS FOR THIS SUCCESS?
One of the key elements of this success is the concentricity of the tool that should not exceed 5 microns. Meeting this requirement will extend the tool life and promote excellent surface finish quality.
· Solid carbide substrate with a high hardness and good toughness.
· Coatings and cutting geometries that are matched to the material hardness.
FINAL RESULTS
The tool cost improvement is significant for all projects by changing to Helion mill tools. The yearly saving is exceeding the project target of 30%.
· The improvement will be duplicated on further 3 existing machines in VCST-BE
Access the product sheet through our ONLINE STORE... References available for inmediate delivery
Tool 926505
Tool 926403
Who can be contacted for more details? Laia Miralta l.miralta@helion-tools.com