COVENTRY TOOLS BITS | CARBIDE BRAZED TURNING TOOLS | |||||||
Co 10% | SPEZIAL | ASP-60 | P-20 | P-40 | K-10 | M-10 | ||
MATERIAL MANUFACTURING | High speed steel 10% Cobalt alloy. First choice quality. | High-speed steel cobalt alloy, Tungsten and Carbon | High alloy ASP-60 powder metallurgical grade with a more even distribution of cobalt, tungsten and Carbide particles.. | Premium carbide imported from Germany and under ISO. | ||||
APPLICATIONS | Turning, grooving and parting off. General purpose cutting tools. | High feed turning. Means cutting depths. | High wear resistance cutting edge. Turning and parting off. | Turning, grooving, threading. Generalmachining. | Turning, grooving, high feed ordificult conditions. | Turning, grooving, threading. Generalmachining. | Turning, grooving, threading. Generalmachining. | |
MACHINING | Tough materials Wood Extrusion Shearing tools |
Tough materials Wood Extrusion Shearing tools |
Carbon steel, stainless steel,aluminium alloys, heat resistant alloys. | First choice grade for general turning steel. | Steel machining under difficult conditions. | Aleaciones de cobre a alta temperatura. Universal grade for cast iron,aluminium, abrasive materials and copper alloys. |
Turning stainless steels and wear resistants manganese steels. | |
RESISTANCE | Allowed in difficult cutting conditions. |
High wear resistance and machining withhigh concentration of heat. | Alta resistencia al desgaste. Alta resistencia de la arista de corte. High wear resistance. High strength cutting edge. |
High wear resistance. | Allowed in difficult cutting conditions. |
High wear resistance. | High wear resistance. | |
REGRINDING | Regrinding easily with ceramic or CBN wheels. | Regrinding easily with ceramic or CBN wheels. | Regrinding easily with ceramic or CBN wheels. | Silicon carbide Wheel, finish withdiamond wheel. | ||||
SPECIAL FEATURES | Good results in wide materials range. |
Better wear resistance at cutting edge. |
Increased productivity by higher cutting conditions and increased wear resistance. |
Optimal performance in machining processes |
Tips
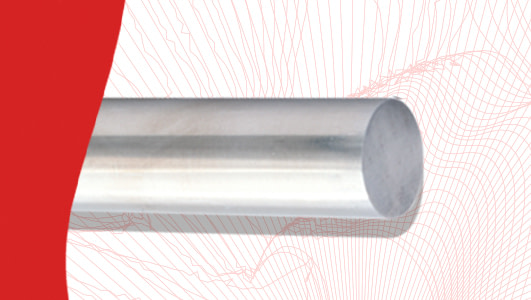
MILLING SOLUTIONS | ||
Problem | Cause | Solutions |
Vibrations on the milling cutter | • Cutting speed is too high • Feed rate is too low • Tool clamping is not unstable • Tool is too long • Tool is too unstable • Flute length too great |
• Reduce cutting speed • Increase feed rate • Check the clamping device or replace • If possible, choose the quickest possible process • Use a stronger shaft • If possible, choose the quickest possible process |
Vibrations on the workpiece | •Clamping is not stable enough | • Check tool clamping and optimize if appropriate |
Cutter breakage | • Tool wear • Incorrect cutting specifications • Vibrations • Conventional milling • Tool stability • Workpiece stability |
• Replace or re-sharpen tool in good time • Match cutting specifications to the work • Reduce rotation speed • Mill in synchronism • If possible, choose the quickest possible process • Check clamping device and optimize if appropriate |
Breakage of the cutting edge | • Tool stability • Workpiece stability • Vibrations • Feed rate is too high • Conventional milling • Cutting material too brittle • Incorrect tool |
• If possible, choose the quickest possible process
• Check clamping device and optimize if necessary• Reduce rotation speed • Reduce feed rate • Mill in synchronism |
Milled slot is too small less than the diameter of the tool | • Too much tool wear | • Replace or re-sharpen tool in good time |
Milled slot is too large less than the diameter of the tool | • Tool run-out error | • Minimize run-out error |
Service life is too short | • Reaming is too intense • Incorrect tool chosen • Incorrect front rake angle • Lip clearance of the tool is incorrect |
• Use a coated tool • Adjust tool to the work • Select a tool with the correct front rake angle • Correctly grind or re-sharpen the tool |
Tool breakage | • Machining cross-section is too large • Feed rate is too high • Tool is too long |
• Reduce or adjust feed rate per tooth • Reduce feed rate • If possible, choose the quickest possible process |
Poor surface quality | • Incorrect tool chosen • Incorrect lubricating coolant delivery • Feed rate is too high • Rotation rate too low • Built-up edge development • Chip removal not at optimum • Chips too large • Tool wear |
• Adjust tool to the work • Ensure correct lubricating coolant delivery • Reduce feed rate • Increase rotation speed • Use tools with a greater twist angle • Optimize lubricating coolant delivery • Reduce machining cross-section • Replace or re-sharpen tool in good time |
Chatter marks on the surface | • Tool run-out error • Tool not stable • Tool clamp unstable |
• Reduce run-out error • Use a tool with a larger shaft • Check the clamping device or replace |
Extreme flank wear | • Machining temperature too high • Incorrect cutting material chosen |
• Reduce cutting speed • Choose a tool made from a suitable cutting material |
Too much tool wear | • Incorrect cutting specifications • Incorrect twist angle • Conventional milling • Incorrect tool |
• Match cutting specifications to the work • Select a tool with the correct twist angle • Use tool in synchronism • Adjust tool to the work |
Lengthways markings on the surface | • Break-outs at the borehole boundary surface | • Replace tool |
Extreme crater wear | • Cutting pressure too high • Machining temperature too high |
• Reduce feed rate • Reduce cutting speed |
DRILLING SOLUTIONS | ||
Problem | Cause | Solutions |
Borehole is too large | • Feed rate is too high • Chipping blockage • Run-out defect on the drill used • Grinds incorrectly |
• Reduce feed rate • Use the correct tool • Reduce run-out defect as much as possible • Check grinding is correct |
Burr at borehole exit | • Cutting speed is too fast • Wear limit width exceeded |
• Reduce feed rate • Replace or re-sharpen tools in good time |
Breakage of the cutting edge | • Unstable working conditions • Incorrect core hole drill • Unstable workpiece clamping • Wear limit width exceeded • Feed rate is too high • Lip clearance angle too great |
• Clear spindle clearance • Use the correct core hole drill • Check workpiece clamping • Replace or re-sharpen tools in good time • Reduce feed rate • Carry out better re-sharpening |
Fissure in the core | • Impact on the chisel edge • Drill tip too sharp • Feed rate is too high • Lip clearance angle too great |
• Correct cutting speed • Re-sharpen correctly • Reduce feed rate • Re-sharpen correctly |
Chisel edge wear | • Cutting speed is too low • Insufficient lubricating coolant delivery • Incorrect lubricating coolant composition • Feed rate is too high |
• Correct cutting speed • Ensure good lubricating coolant delivery • Ensure good lubricating coolant composition • Reduce feed rate |
Built-up edge development | • Insufficient lubricating coolant delivery • Incorrect lubricating coolant composition • Cutting speed is too low • Uncoated tool |
• Ensure good lubricating coolant delivery • Ensure good lubricating coolant composition • Increase cutting speed • Use a coated tool |
Poor borehole surface quality | • Feed rate is too low • Inaccurate positioning |
• Increase feed rate • Centre borehole in advance |
Vibrations | • Cutting speed is too high • Feed rate is too low • Unstable workpiece clamping • Run-out error of the core hole drill is too great |
• Reduce cutting speed • Increase feed rate • Ensure stable workpiece clamping • Reduce run-out error |
Flank wear | • Cutting speed is too high • Feed rate is too low • Clearance angle too small |
• Reduce cutting speed • Increase feed rate • Increase clearance angle |
Corner wear | • Excessive speed | • Reduce speed to the optimum • Possible increase in feed rate |
Margin wear | • Cutting speed is too high • Run-out error of the core hole drill is too great • Tool tapering is insufficient • Insufficient lubricating coolant delivery • Incorrect lubricating coolant composition |
• Reduce cutting speed • Reduce run-out error • Use tools that are more tapered • Ensure good lubricating coolant delivery • Ensure good lubricating coolant composition |
Fluting edge breakage | • Poor chip removal • Drill bit is not stable in the chuck |
• Remove earlier • Ensure that the drill bit is in the chuc |
Stand length is insufficient | • Incorrect cutting specifications • Unstable workpiece clamping • Insufficient lubricating coolant delivery • Incorrect lubricating coolant composition |
• Ensure cutting specifications are correct • Ensure stable workpiece clamping • Ensure good lubricating coolant delivery • Ensure good lubricating coolant composition |
Poor borehole surface quality | • Feed rate is too low • Inaccurate positioning |
• Increase feed rate • Centre borehole in advance |
Vibrations | • Cutting speed is too high • Feed rate is too low • Unstable workpiece clamping • Run-out error of the core hole drill is too great |
• Reduce cutting speed • Increase feed rate • Ensure stable workpiece clamping |
Flank wear | • Cutting speed is too high • Feed rate is too low • Clearance angle too small |
• Reduce cutting speed • Increase feed rate • Increase clearance angle |
Corner wear | • Excessive speed | • Reduce speed to the optimum • Possible increase in feed rate |
Margin wear | • Cutting speed is too high • Run-out error of the core hole drill is too great • Tool tapering is insufficient • Insufficient lubricating coolant delivery • Incorrect lubricating coolant composition |
• Reduce cutting speed • Reduce run-out error • Use tools that are more tapered • Ensure good lubricating coolant delivery • Ensure good lubricating coolant composition |
Fluting edge breakage | • Poor chip removal • Drill bit is not stable in the chuck |
• Remove earlier • Ensure that the drill bit is in the chuc |
Stand length is insufficient | • Incorrect cutting specifications • Unstable workpiece clamping • Insufficient lubricating coolant delivery • Incorrect lubricating coolant composition |
• Ensure cutting specifications are correct • Ensure stable workpiece clamping • Ensure good lubricating coolant delivery • Ensure good lubricating coolant composition |
THREADING SOLUTIONS | ||
Problem | Cause | Solutions |
Thread cutting | • Incorrect thread cutter • Incorrect tolerance • Thread cutter is not centered • Cutting speed is too high • Insufficient lubricating coolant delivery • Core hole bore is too small • Chipping blockage • Incorrect axial feed rate selected |
• Match the thread cutter to the correct material group • Check the tolerance of the thread cutter and, if applicable, use another tool • Check tool mount and position the center of the thread cutter over the hole • Reduce cutting speed • Ensure good lubricating coolant delivery • Ensure that the correct core hole bore is used (see core hole drill table) • Use the correct tool shape • Reduce feed rate to 5-10% and check the contact pressure of the thread cutter |
Thread is too narrow | • Incorrect thread cutter • Incorrect tolerance • Core hole bore is too small • Thread is too narrow |
• Match the thread cutter to the correct material group • Check the tolerance of the thread cutter and, if applicable, use another tool • Ensure that the correct core hole bore is used (see core hole drill table) • Ensure that the correct tool shape is used |
Too much wear | • Incorrect thread cutter • Insufficient lubricating coolant delivery • Incorrect lubricating coolant composition • Cutting speed is too high |
• Match the thread cutter to the correct material group and select the correct shape • Ensure good lubricating coolant delivery • Ensure correct lubricating coolant composition • Reduce cutting speed |
Tool chipping off | • Incorrect thread cutter • Hardened surface • Core hole bore is too narrow • Insufficient lubricating coolant delivery • Incorrect lubricating coolant composition |
• Match the thread cutter to the correct material group and select the correct shape • Reduce speed, choose a coated tool, • Ensure good lubricating coolant composition • Ensure that the correct core hole bore is used (see core hole drill table) • Ensure good lubricating coolant delivery • Ensure correct lubricating coolant composition |
Thread surface is not clean | • Chipping blockage • Cold welding on the thread cutter flank • Unsuitable tool shape • Cutting speed is too high • Insufficient lubricating coolant delivery • Incorrect lubricating coolant composition |
• Ensure that the correct tool shape is used • Remove cold welding or use another tool • Ensure the correct thread cutter is used • Reduce cutting speed • Ensure good lubricating coolant delivery • Ensure correct lubricating coolant composition |
Thread cutter breakage | • Chip blockage or jam • Tool shape unsuitable for the work • Too much wear on the thread cutter • Torque is too high • Thread core hole is too narrow |
• Adapt choice of thread cutter to the work being carried out • Ensure that the correct tool shape is used • Replace the thread cutter in good time • Use a thread cutter with overload coupling • Ensure that the correct core hole bo |
Thread cutter overheating | • Insufficient lubricating coolant delivery • Incorrect lubricating coolant composition • Thread cutter is worn |
• Ensure good lubricating coolant delivery • Ensure correct lubricating coolant composition • Replace the thread cutter in good time |
Thread axially blended | • Obtain left-rotating thread cutter for lower point pressure • Strong right-rotating thread cutters have point pressure that is too strong |
• Keep thread cutter in the same pressure range as the thread cutter chuck. Stronger axial contact pressure when beginning to cut • Only minimum contact pressure when beginning to cut |
REAMING SOLUTIONS · SOLUCIONES PARA ESCARIADO | ||
Problem | Cause | Solutions |
Diameter is too large | • Cutting speed is too high • Feed rate is too high • Insufficient lubricating coolant delivery • Incorrect lubricating coolant composition • Point is too short or very uneven • Tool or machine spindle rotation incorrect • Due to low-density or flexible structure, the working material enlarges |
• Reduce cutting speed • Reduce feed rate • Ensure good lubricating coolant delivery • Ensure correct lubricating coolant composition • Lengthen point or reduce point angle • Centrally clamp or guide the reamer. Use a reamer chuck |
Diameter is too narrow |
• Cutting speed is too low • Feed rate is too low • Chip removal rate is too low • Point is too long • Tool is ground smooth • The working material is of high density or has an inflexible structure • Reamer of insufficient size • Too much heat created when reaming. Contracting borehole • Tool diameter too small |
• Increase cutting speed • Increase feed rate • Increase machining allowance • Select a smaller point • Check the tool and replace in good time • Increase reamer diameter • Select a higher allowance • Increase lubricating coolant delivery • Select the correct diameter |
Heavy wear | • Insufficient size | • Select a larger diameter |
borehole is not round or is conical | • Incorrect positioning in the machine spindle • Alignment error between the tool and the borehole • Asymmetrical point angle • Incorrect tool run-out • Clearance angle too great • Point is not round • Insufficient guide |
• Check the spindle and correct its position • Use front-cutting reamers • Re-sharpen point angle • Centrally clamp tool, use reamer chuck and guide • Reduce clearance angle when re-sharpening • Evenly sharpen and round the point • Guide more accurately or use guide reamers |
Poor surface quality | • Worn tool • Front rake angle is too small • Cutting speed is too low • Feed rate is too low • Workpiece tends to stick (built-up edge) • Cutting exit is sharp-edged • Insufficient lubricating coolant delivery • Incorrect lubricating coolant composition • Cutting is uneven • Defective point |
• Replace or re-sharpen tool in good time • Re-sharpen correctly • Increase cutting speed • Increase feed rate • Increase clearance angle and front rake angle; use highly fluid lubricant • Round and smooth the borehole exit • Ensure good lubricating coolant delivery • Ensure correct lubricating coolant composition • Grind the point and guide piece to an evenly round shape or to a tapered shape • Finely smooth or lap the point round and smooth the guide piece joint |
The tool jams and breaks | • Borehole is too narrow • Bevel width is too great • Shaft is too short • Worn tool |
• Reduce material cross-section • Check the tool and replace if necessary • Check the tool and replace if necessary • Replace or re-sharpen tool in good time |
Borehole exit too narrow | • Feed rate when removing the reamer from the borehole is too high | • Reduce feed rate shortly before passing through or use even feed rate |
Broken off or deformed driver | • Incorrect position between shaft and clamping device | • Keep shaft and clamping device clean and undamaged |